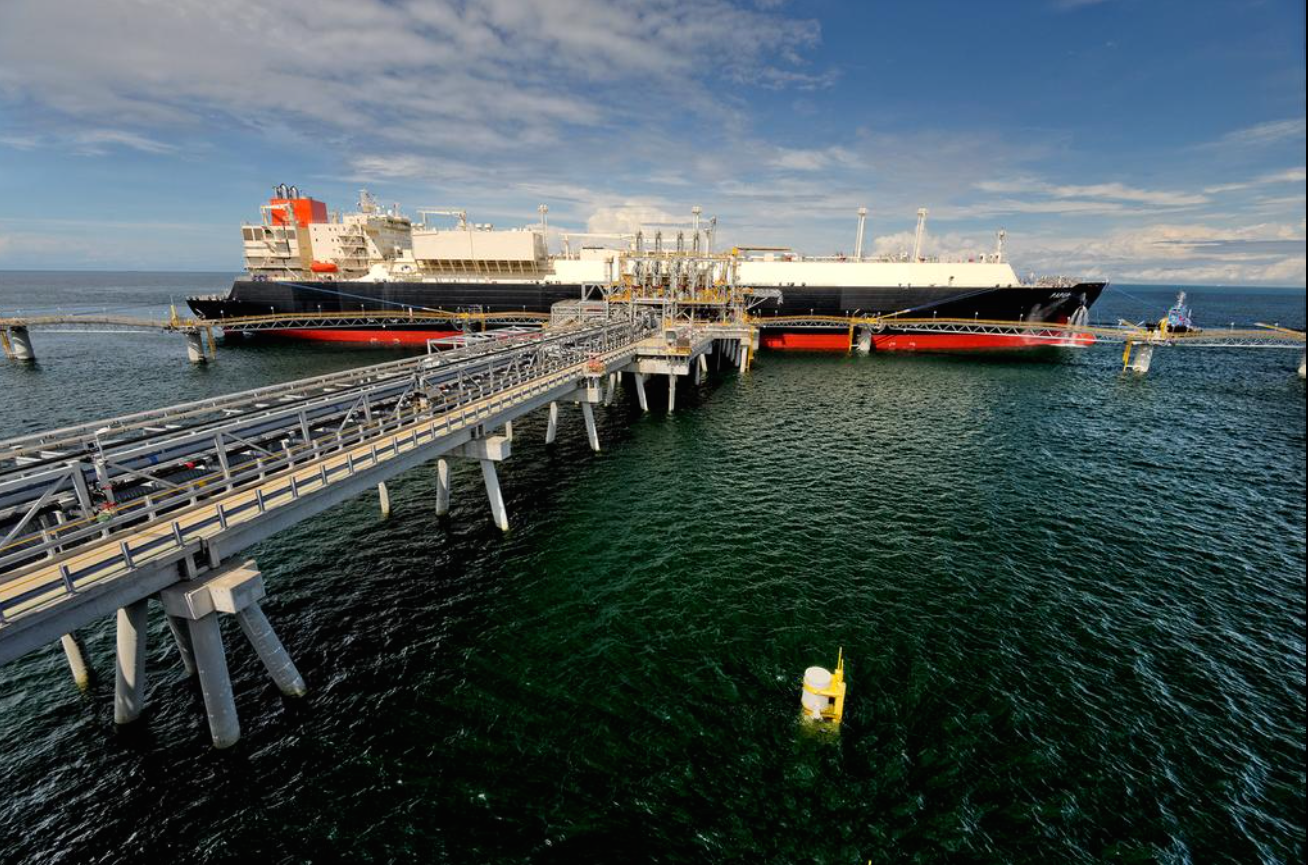
An Overview of LNG
What is LNG?
LNG, or Liquefied Natural Gas, is a natural gas that is predominantly methane which has been converted to liquid form for the convenience of transportation and storage. Liquefying of the natural gas approximately reduces the volume by 1/600th. LNG is colorless, odorless, and non-toxic. The liquefaction process consists of the removal of components such as heavy liquids, CO2, H2S, brine, mercury, and any other lighter hydrocarbons leaving methane and ethane remaining. Once impurities are removed, the natural gas is cooled to -260 F (-162 C).

Extraction
With the combination of buried organic matter, heat, compression, and time- gas becomes trapped in the pores of rocks. Wells are created where these gases are extracted thousands of meters beneath the surface. One method that has been developed is called fracking. The process begins by drilling a few kilometers underground followed by changing the direction of the drill horizontally. The drill can be turned in different directions so that only one hole is needed to reach multiple areas in the ground. The wellbore is sealed by cement (casing) so no underground gases can escape. Fracking fluid is released which helps in the fracturing of the earth. The trapped gas is released where it can travel up the pipe towards the surface. The fluid is mostly sand, water, and chemicals. Once collected, the gas is sent via pipeline to LNG processing plants. The collected natural gas goes through a series of processes where all unwanted components get filtered and removed:
-
Slug Catcher-separates condensate from the gas
-
Acid Gas Removal Unit- removal of CO2
-
Dehydration Unit- removal of H2O
-
Mercury Removal Unit- mercury is absorbed by carbon granules
-
Flows through refrigerant and heat exchanger
-
Scrub Column- cold liquid mist removes the heavier hydrocarbons
-
Flows through main cryogenic heat exchanger
-
Runs through flash vessels where gas is cooled to -150°C @2-5 atm
-
Final flash vessel cools gas to -162°C @ atmospheric pressure
-
Transported to storage tank via pipes and stored at -162°C
Three types of cargo tanks:
Self-Supporting Spherical
Self-Supporting Prismatic
Membrane
LNG Processing Plant --> Ship
In over 50 years, there has not been any major accidents with a LNG carrier globally. Even if LNG was to leak, it would stay on top of the water where it will disperse into the air harming no aquatic life. A standard LNG ship has four to seven tanks located near the median of the ship. Inside each tank, there are 3 submerged pumps. Two of which consist of main cargo pumps which are designed for cargo transfer and the third is referred to as the spray pump. The spray pumps are used to extract the LNG to be used as fuel by vaporization or for cooling the tanks. These pumps are located at top and runs through the entire depth of the tank. Normally, it takes about a whole day to fill up the tanks.
Before the LNG can be transferred, the tanks must be filled with air. This allows for maintenance on the pumps and the tank. The liquid cargo cannot be loaded directly, otherwise the existence of oxygen or other gases within the tank could cause an explosive reaction or cause damage to the ship as a result of the sudden change in temperature from the LNG. An inert gas is burned to produce carbon dioxide in order to stabilize the oxygen level under 5%. Once the oxygen is removed, the remaining carbon dioxide must also then be removed for it will freeze under low temperature. LNG is taken to the main vaporizer where it is heated until it is back in a gaseous state. Once warmed to about 20°C, the gas is blown into the tanks in order to displace the inert gas until it is all removed.
After CO2 and O2 are removed, the next stage of the process is referred to as the
cool down”. Using spray heads, the LNG is sprayed into the tank. The temperature difference vaporizes the LNG, however, it cools the tank at the same time. Once the tank reaches -140°C, the LNG can be loaded in bulk. From the pipes onshore, LNG is transferred into the vessel until it reaches about 98% full. The extra vacant space is necessary because of expansion/contraction of the gas.
During voyage, boil-off strategies have been developed to provide steam for propulsion. Depending on the design/type of the ship, leftover gas can be re-liquefied and stored back into the tanks. The tanks onboard are designed similar to a vacuum flask, or thermos, for the highest possible insulation in order to keep the temperature static. Tanks can be powered by steam turbines with boilers that are dual fueled (use oil or methane). The choice of fuel is determined typically by the distance of travel and the price of LNG and oil.
Ship --> Land
Once the LNG carrier has made it to the destination port, the LNG is piped out of the ship into specialized regasification facilities where it was warmed back up to above 0°C into gas phase. Most common method of re-heating LNG is the use of seawater. From there, it is sent to the energy grid to provide power for homes, buildings, and vehicles.
Inside completed membrane tank. Human for size comparison
If we were to make the transition to using LNG as a main source of power, there could be a huge difference in the amount of emission and pollution towards the atmosphere. Countries in Asia, e.g. China and India, rely most of their power generation from coal. Switching to a cleaner fuel, such as LNG, can result in health benefits throughout their country. In China, millions of people have died due to premature death from air pollution. That could change if the use of a cleaner fuel were to take place. Also, not only does China’s pollution effect themselves, but also nearby countries where pollution can travel by downward wind. If we were to send our natural gas to China, India, or any other heavy-fuel country, we able be able to address more on the issue with the addition of making revenue back to our own.
Night photo of LNG plant in Qatar


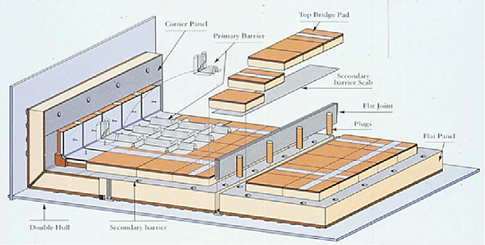
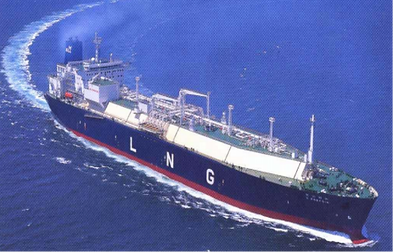


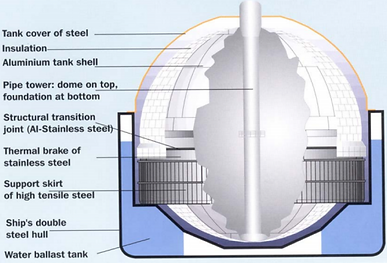

Interior of membrane tank. Human standing to provide scaled comparison.
